Macleay Island house
CM Architects created this design of a new holiday home that can be constructed in a number of modules and installed over a number of years.
The client wanted to maximise the water front views and provide a low key, bushland and water front focused holiday home for them and their children.
Materials will be low maintenance and integrated with the surrounding landscape.
Site constraints include flood, waterfront and landslide overlays as well as remoteness of the site for construction and transport of materials. For this reason, the client considered modular off site construction in elements or components that can fit onto either a barge or large trucks that could be ferried to the site.
Due to the proposal to build the ground floor first and then the upper floor in the future, the structure was designed to be ready for and accommodate the later installation of the upper floor and we therefore proposed a 600mm gap between the lower and upper floors which also provides a visual separation between the 2 stages and also provides a breezeway between the 2 levels to cool and allow natural breezes to infiltrate the design and the spaces providing natural ventilation throughout the year.
The proposed east elevation- was designed to capture the morning sun and water views throughout the day. Long overhangs were introduced to reduce heat gain and sliding stacking doors to open up the entire front of the house in good weather out to the east deck. Built in seating dropped below floor level either side of stairs down to the water provides a casual relaxing area closer to the water.
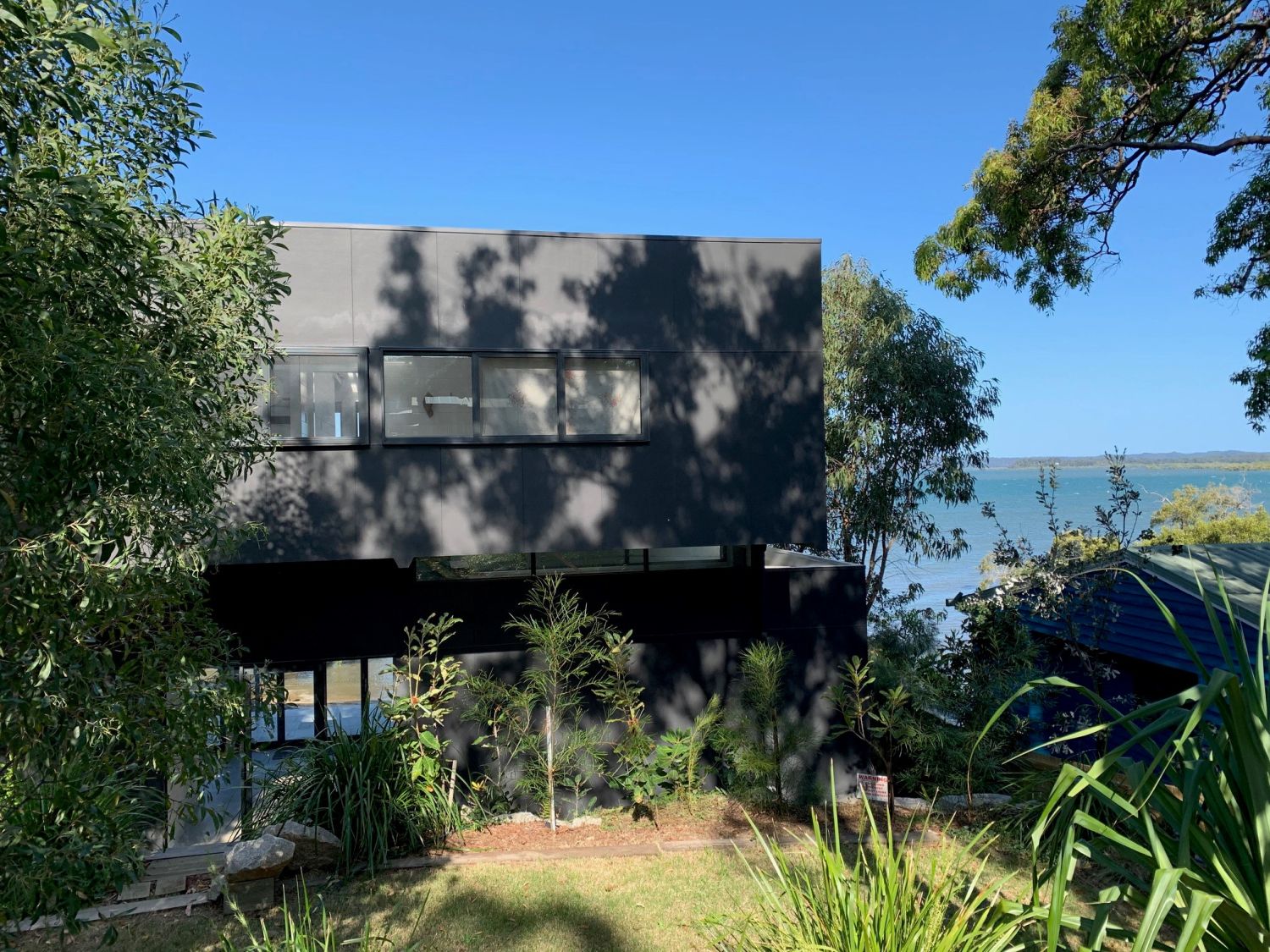